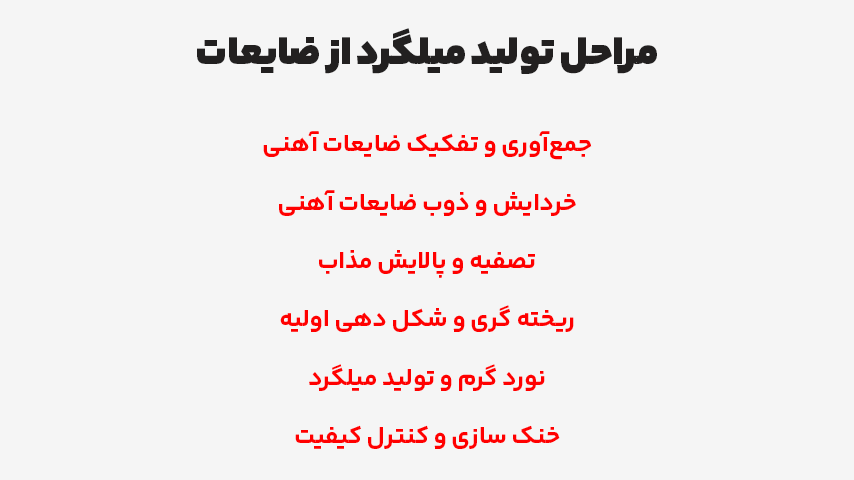
تولید میلگرد از ضایعات فواید بسیاری برای محیط زیست دارد .استفاده از ضایعات فلزی در تولید میلگرد یکی از روشهای مؤثر برای کاهش هزینهها، حفظ منابع طبیعی و کاهش آسیبهای زیست محیطی است. در این روش ضایعات آهنی بازیافت شده و پس از پردازش به میلگردهای استاندارد تبدیل می شوند. قیمت میلگر د هم به روش تولید و سطح کیفیت محصول بستگی دارد .با کفیفت ترین میلگرد ها با تنوع سای زو برند در بازرگانی آهن جم عذضه میشوند .جهت مشاده قیمت میلگرد آهن جم اینجا را لمس کنید .
تولید میلگرد از ضایعات شامل مراحل مختلفی است که در ادامه به طور کامل بررسی خواهیم کرد.در ابتدا ویدیو تولید میلگرد از ضایعات قرار گرفته است .
مراحل تولید میلگرد از ضایعات
برای تولید میلگرد از ضایعات باید مراحل زیر طی شود .
جمعآوری و تفکیک ضایعات آهنی
جمع آوری ضایعات اولین و مه مترین مرحله در فرآیند تولید میلگرد از مواد بازیافتی است. این ضایعات از منابع مختلفی مانند کارخانه های صنعتی، خودروهای فرسوده، ساختمانهای تخریبی و ابزارآلات مستعمل به دست میآیند. در این مرحله ضایعات فلزی از دیگر مواد زائد مانند پلاستیک و چوب جدا سازی می شوند.
پس از جمعآوری تفکیک ضایعات بر اساس نوع آلیاژ و میزان ناخالصی انجام میشود. این کار به بهبود کیفیت مواد اولیه و جلوگیری از مشکلاتی مانند کاهش استحکام میلگرد تولیدی کمک می کند. تفکیک ضایعات به روشهای دستی، مغناطیسی و با استفاده از دستگاههای پیشرفته انجام میشود.
خردایش و ذوب ضایعات آهنی
پس از تفکیک ضایعات آهنی وارد مرحله خردایش میشوند. در این مرحله قطعات بزرگ فلزی با دستگاههای خرد کن به قطعات کوچک تر تبدیل می شوند تا ذوب آنها راحت تر انجام شود. اندازه مناسب ضایعات باعث افزایش راندمان ذوب و کاهش مصرف انرژی در کوره ها میشود.
سپس ضایعات آهنی خرد شده در کورههای قوس الکتریکی یا کورههای القایی ذوب میشوند. در این مرحله ناخالصی هایی مانند کربن اضافی، فسفر و گوگرد از فلز جدا شده و مواد افزودنی لازم برای بهبود خواص مکانیکی میلگرد به مذاب اضافه میشود. دمای ذوب معمولاً بین ۱۵۰۰ تا ۱۶۰۰ درجه سانتی گراد است.
تصفیه و پالایش مذاب
برای دستیابی به کیفیت بالاتر مذاب آهنی باید تصفیه شود. در این مرحله ترکیبات نامطلوب از فلز جدا شده و درصد عناصر آلیاژی تنظیم می شود. تصفیه مذاب از طریق روشهایی مانند گاز زدایی، تزریق اکسیژن و استفاده از فلاکس های شیمیایی انجام میشود.
پالایش دقیق مذاب باعث افزایش استحکام، انعطاف پذیری و مقاومت به خوردگی میلگرد نهایی میشود. این مرحله نقش حیاتی در تضمین کیفیت محصول نهایی دارد و تأثیر مستقیمی بر استانداردهای میلگرد تولیدی خواهد داشت.
ریخته گری و شکل دهی اولیه
پس از تصفیه، مذاب آهنی در قالبهای مخصوص ریخته گری شده و به شکل شمش های فولادی (بیلت) در میآید. این بیلتها پس از سرد شدن برای مرحله نورد آماده می شوند. کیفیت بیلت تأثیر مستقیمی بر ویژگیهای مکانیکی میلگرد خواهد داشت.
بیلتهای تولید شده معمولاً دارای ابعاد استانداردی هستند و باید قبل از ورود به مرحله نورد مورد بررسی کیفی قرار گیرند. وجود ترک یا حفره در سطح بیلت میتواند کیفیت میلگرد را کاهش داده و منجر به مشکلات ساختاری شود.
نورد گرم و تولید میلگرد
در این مرحله بیلتهای فولادی در کورههای مخصوصی تا دمای حدود ۱۲۰۰ درجه سانتی گراد گرم میشوند و سپس وارد دستگاههای نورد می شوند. در فرآیند نورد گرم بیلتها تحت فشار قرار گرفته و به تدریج به شکل میلگردهای استاندارد تبدیل می شوند.
پس از رسیدن به قطر مناسب سطح میلگردها برای بهبود چسبندگی با بتن طرحدار (آجدار) میشود. این آج ها باعث افزایش استحکام و یکپارچگی سازههای بتنی میشوند. پس از این مرحله میلگردهای تولیدی به طول های مشخص برش داده شده و برای سرد شدن به مرحله نهایی انتقال مییابند.
خنک سازی و کنترل کیفیت
میلگردهای تولیدی پس از نورد گرم باید به صورت کنترل شده خنک شوند تا خواص مکانیکی مطلوبی داشته باشند. خنک سازی معمولاً به روش های کنترل شده مانند خنک سازی در هوای آزاد یا استفاده از سیستم های پاشش آب انجام میشود.
پس از خنک سازی میلگردها از نظر ابعاد، استحکام کششی، انعطاف پذیری و چسبندگی به بتن آزمایش میشوند. آزمایش های استاندارد کنترل کیفیت تضمین میکنند که میلگردهای تولیدی مطابق با استانداردهای ملی و بین المللی هستند.
بسته بندی و ارسال میلگرد به بازار
پس از تأیید کیفیت میلگردها در بسته بندیهای استاندارد قرار گرفته و آماده ارسال به بازار مصرف میشوند. بسته بندی مناسب باعث سهولت در حمل ونقل و جلوگیری از آسیب های فیزیکی در حین جا به جایی میشود.
میلگردهای بازیافتی از ضایعات علاوه بر کاهش هزینههای تولید، به حفظ محیط زیست نیز کمک میکنند. این روش باعث کاهش مصرف منابع طبیعی و انرژی میشود و یک گزینه پایدار و اقتصادی برای صنعت ساخت وساز محسوب میشود.
چه ضایعاتی برای تولید میلگرد مناسب است ؟
برای تولید میلگرد ضایعات فلزی که دارای مقدار بالایی از آهن و ترکیبات قابل بازیافت هستند مناسبند. مهم ترین این ضایعات شامل قراضههای آهن، تیرآهنها و میلگردهای فرسوده، بدنه خودروهای اسقاطی، ورقهای فولادی، لوازم خانگی کهنه، ضایعات صنعتی و حتی آهن آلات تخریب شده از ساختمان های قدیمی میشود. این مواد پس از جمع آوری به دقت تفکیک میشوند تا ناخالصی هایی مانند رنگ، پلاستیک، چوب یا سایر فلزات نامناسب حذف شوند. ضایعات باکیفیت باعث تولید میلگردهایی با استحکام بالا و مطابق با استانداردهای صنعتی میشوند.
علاوه بر این ضایعات چدنی و فولادهای آلیاژی نیز در برخی موارد برای تولید میلگردهای خاص مورد استفاده قرار میگیرند. با این حال برای تولید میلگرد استاندارد ساختمانی میزان عناصر آلیاژی باید در حد متعادل باشد تا محصول نهایی از نظر جوش پذیری و مقاومت مکانیکی کیفیت مطلوبی داشته باشد. ضایعاتی که دارای مقدار زیادی روی، مس یا سایر عناصر غیرمجاز باشند، ممکن است کیفیت میلگرد را کاهش دهند بنابراین در مرحله فرآوری و ذوب باید کنترل دقیقی روی ترکیب شیمیایی آنها انجام شود.
روش های تولید میلگرد از ضایعات
نورد گرم
نورد گرم رایج ترین روش تولید میلگرد است که در آن شمشهای فولادی (بیلت) تا دمای حدود ۱۲۰۰ درجه سانتی گراد گرم شده و سپس از میان مجموعه ای از غلتکها عبور داده میشوند تا به قطر مورد نظر برسند. این فرآیند باعث تغییر شکل پلاستیک فلز شده و ساختار دانه بندی فولاد را بهبود می بخشد. در انتهای خط تولید میلگردها تحت عملیات خنک کاری کنترل شده قرار میگیرند تا استحکام مکانیکی آنها افزایش یابد.
میلگردهای تولید شده به روش نورد گرم معمولاً در صنایع ساختمانی و سازههای بتنی مورد استفاده قرار میگیرند. این میلگردها دارای استحکام و انعطاف پذیری بالایی هستند و به دلیل شکل دهی در دمای بالا، دارای مقاومت مناسبی در برابر تنش های فشاری و کششی هستند. میلگردهای آجدار که برای افزایش چسبندگی با بتن طراحی شدهاند عمدتاً از طریق این روش تولید میشوند.
نورد سرد
در روش نورد سرد میلگرد از بیلتهای فولادی که در دمای محیط یا کمی بالاتر از آن قرار دارند تولید میشود. در این روش فولاد بدون نیاز به حرارت دهی تحت فشار غلتک ها شکل داده میشود که باعث افزایش استحکام تسلیم و مقاومت کششی آن میشود. نورد سرد معمولاً برای تولید میلگردهای با دقت بالا در قطر و ابعاد به کار می رود و سطح میلگرد های تولیدی از این روش صاف و براقتر از میلگردهای نورد گرم است.
به گفته آهن جم :تولید میلگرد با نورد سرد بیشتر در قدیم متداول بوده است .در این روش با استفاده از فشار و کشش باعث در هم شکستن و به هم ریختگی ساختار شمش می شوند .تولید میلگرد به روش نورد سرد تا پایان مرحله رافینگ که به کوچک و گرد کردن تقریبی سطح مقطع شمش فولادی میپردازند مانند فرایند نورد گرم انجام می شود.
میلگردهای نورد سرد بیشتر در صنایع حساس مانند ساخت قطعات دقیق مهندسی، تولید سیمهای فولادی و در برخی از بخشهای سازههای خاص مورد استفاده قرار میگیرند. این نوع میلگردها به دلیل سخت شدن در فرآیند شکل دهی کمتر انعطاف پذیر بوده و برای کاربردهایی که نیاز به خم کاری دارند چندان مناسب نیستند.
روش میکرو آلیاژی (ترمکس)
در روش ترمکس،میلگردهای تولید شده از فرآیند نورد گرم بلافاصله پس از خروج از غلتک ها تحت آب دهی سریع (کویینچینگ) قرار میگیرند. این فرآیند باعث ایجاد لایه ای سخت در سطح میلگرد شده در حالی که بخش داخلی آن نرم و انعطاف پذیر باقی می ماند. پس از خنک کاری سریع میلگرد به تدریج در هوای آزاد گرم میشود که این فرآیند باعث متعادل شدن سختی و استحکام آن میشود.
میلگردهای ترمکس معمولاً در پروژههای ساختمانی و عمرانی که نیاز به استحکام بالا و مقاومت در برابر زلزله دارند مورد استفاده قرار می گیرند. این میلگردها نسبت به میلگردهای معمولی استحکام بیشتری داشته و در عین حال شکل پذیری مناسبی دارند. همچنین به دلیل کاهش میزان کربن در ترکیب شیمیایی جوش پذیری بهتری نسبت به میلگردهای آلیاژی دارند.
به گفته آهن جم : ترمکس یکی از روش های تولید میلگرد می باشد.در فرایند ترمکس میلگرد های تولید شده طی فرایند نورد گرم را داخل آب قرار میدهند تا سطح رویی خنک شده و مرکز میلگرد نیز با گذشت زمان خنک می شود. همین امر باعث ایجاد ویژگی هایی در میلگرد میشود .
میلگرد ترمکس با توجه به نحوه ساخت مقاومت بسیار بالایی دارد. مقاومت بالای میلگرد ترمکس مزایا و معایبی را در این محصول به وجود آورده است. بنای تولید میلگرد به روش ترمکس تکنولوژی به نام QST می باشد
روش آلیاژی
در روش تولید میلگرد آلیاژی به مذاب فولاد در حین تولید عناصر آلیاژی مانند وانادیم، کروم، مولیبدن و نیکل اضافه میشود تا خواص مکانیکی آن بهبود یابد. این نوع میلگردها بدون نیاز به عملیات ترمکس و کوئینچینگ در همان فرآیند ریخته گری و نورد به استحکام و انعطاف پذیری مطلوب میرسند.
میلگردهای آلیاژی معمولاً در سازههای حساس مانند پلها، ساختمانهای بلند مرتبه، سدها و نیروگاهها استفاده میشوند. این میلگردها مقاومت بالایی در برابر خوردگی، سایش و ضربه دارند و برای مناطق زلزله خیز یا شرایط محیطی سخت مناسب محسوب میشوند.
تولید از ضایعات فلزی
در این روش میلگرد از بازیافت ضایعات فلزی مانند قراضههای آهن، خودروهای فرسوده و ضایعات صنعتی تولید میشود. ابتدا ضایعات جمع آوری و تفکیک شده و پس از خرد شدن در کورههای قوس الکتریکی یا القایی ذوب میشوند. سپس مذاب فولادی تصفیه شده و در قالبهای مخصوص ریختهگری شده و فرآیند نورد بر روی آن انجام میشود تا میلگرد نهایی شکل بگیرد.
این روش علاوه بر کاهش هزینههای تولید به کاهش مصرف مواد خام و حفظ منابع طبیعی کمک میکند. میلگردهای تولید شده از ضایعات معمولاً در پروژههای ساختمانی و عمرانی با هزینه های پایین تر استفاده میشوند. البته برای تضمین کیفیت این میلگردها باید مطابق با استانداردهای لازم کنترل شوند تا از استحکام کافی برخوردار باشند.
کوره های مناسب برای ذوب ضایعات
کوره قوس الکتریکی (Electric Arc Furnace - EAF)
کوره قوس الکتریکی یکی از پرکاربرد ترین تجهیزات برای ذوب ضایعات فولادی در صنایع فولاد سازی است. در این کوره با استفاده از جریان الکتریکی قوس بین الکترود ها و ضایعات فولادی ایجاد میشود که باعث ذوب فلز میگردد. این کوره به دلیل توانایی در کنترل دما و سرعت ذوب یکی از انتخاب های اصلی در تولید میلگرد راف است. همچنین امکان استفاده از ضایعات فولادی مختلف به عنوان مواد اولیه از مزایای آن به حساب میآید. از آنجا که ضایعات فولادی عمدتاً دارای ترکیب شیمیایی متنوعی هستند کوره قوس الکتریکی قادر است تا دما و شرایط ذوب را تنظیم کند تا کیفیت محصول نهایی حفظ شود.
در عمل کورههای قوس الکتریکی معمولاً دارای یک یا چند الکترود گرافیتی هستند که به محفظه کوره وارد میشوند. جریان الکتریکی به این الکترودها اعمال میشود و قوس الکتریکی تشکیل میدهد. دمای ایجاد شده در قوس به حدی بالا می رود که فولاد را ذوب میکند. این فرآیند به دلیل استفاده از انرژی برق به راحتی قابل کنترل است و امکان بازیابی ضایعات فولادی را فراهم میکند. این کورهها به دلیل هزینه های عملیاتی کمتر نسبت به روش های دیگر مانند کوره بلند محبوب هستند و به دلیل بازده بالا در بسیاری از کارخانه های فولاد سازی برای تولید میلگرد و دیگر محصولات فولادی به کار میروند.
کوره القائی (Induction Furnace)
کوره القائی نیز یک روش موثر و کارآمد برای ذوب ضایعات فولادی است که به دلیل دقت بالا و کنترل فرآیند در صنایع فولاد سازی برای تولید میلگرد راف بهکار میرود. این کورهها از جریان های الکتریکی متناوب برای ایجاد میدان مغناطیسی و ذوب مواد استفاده میکنند. در این فرآیند زمانی که جریان الکتریکی از یک سیم پیچ عبور میکند میدان مغناطیسی ایجاد میشود که باعث جریانهای گردابی در فلز میشود و در نتیجه حرارت تولید شده موجب ذوب شدن فولاد میگردد. این روش علاوه بر ایجاد دمای بالا و ذوب سریع موجب کاهش تلفات انرژی نیز میشود.
مزیت کورههای القائی نسبت به کورههای دیگر دقت بالا در تنظیم دما و فرآیند ذوب است. این کورهها توانایی ذوب فلزات با ترکیب شیمیایی خاص را دارند که این ویژگی در تولید میلگرد راف با خواص فنی خاص از اهمیت بالایی برخوردار است. کورههای القائی همچنین تمایل دارند به دلیل نداشتن آلودگی ناشی از گازهای کورهای نسبت به کوره های قوس الکتریکی یا کوره بلند تمیزتر باشند. با این حال این کورهها به دلیل هزینه های نصب و راه اندازی بیشتر در کارخانه های کوچک و متوسط که به دنبال دقت و بهره وری بیشتر هستند استفاده میشوند.
کوره بلند (Blast Furnace)
کوره بلند یکی از قدیمی ترین روشها برای تولید فولاد است که بیشتر برای ذوب سنگ آهن استفاده میشود اما در برخی موارد برای ذوب ضایعات فولادی نیز کاربرد دارد. در این کوره مواد اولیه شامل سنگ آهن، کک و سنگ آهک وارد میشود و در دمای بسیار بالا (بالای ۱۰۰۰ درجه سانتی گراد) ذوب میشود. گرچه این کوره معمولاً برای تولید فولاد از سنگ آهن استفاده میشود میتواند برای ذوب ضایعات فولادی در مقیاسهای بزرگ نیز به کار رود. ضایعات فولادی وارد کوره بلند میشوند و با استفاده از گرمای حاصل از سوخت کک به فولاد مذاب تبدیل میشوند.
مزیت کوره بلند در مقیاس بزرگ تولید است. این کورهها می توانند مقدار زیادی فولاد را در یک بار ذوب کنند و بنابراین برای کارخانههایی که نیاز به تولید انبوه دارند گزینه مناسبی هستند. اما از آنجا که کوره بلند معمولاً به انرژی زیادی نیاز دارد و فرایند پیچیده تری دارد برای تولید میلگرد راف و استفاده از ضایعات فولادی در مقیاس کوچک یا متوسط چندان کارآمد نخواهد بود. به همین دلیل این کوره بیشتر در شرایطی که تولید فولاد از سنگ آهن به همراه ذوب ضایعات فولادی در مقیاسهای بزرگ لازم باشد مورد استفاده قرار میگیرد.
کوره پخت (Induction Melting Furnace)
کوره پخت یا همان کوره القائی به طور مشابه به کورههای القائی عمل میکند اما با تمرکز بیشتر بر روی ذوب و پخت ضایعات فولادی با دقت بالا و در حجمهای کوچکتر. در این نوع کوره از اصول میدان مغناطیسی برای ایجاد جریانهای الکتریکی در ضایعات فولادی استفاده میشود. این جریانها باعث گرم شدن ضایعات و ذوب شدن آنها در دمای بالا میشود. مزیت این کورهها این است که دمای ذوب و زمان فرآیند قابل کنترل است که این ویژگی باعث میشود که برای تولید میلگرد راف با کیفیت بالا مناسب باشد. همچنین این کورهها به دلیل نداشتن آلودگی گازهای سمی از نظر زیست محیطی نیز ترجیح داده میشوند.
کیفیت میلگرد تولید شده از ضایعات
کیفیت میلگردهای تولید شده از ضایعات فولادی به چند عامل بستگی دارد که مهمترین آنها فرآیند ذوب و تصفیه مواد اولیه است. در صورتی که ضایعات فولادی از منابع مختلف و با ترکیب شیمیایی متفاوت جمع آوری شده باشند میتوانند باعث تغییرات در ترکیب نهایی فولاد و خواص مکانیکی میلگرد شوند. اگر فرآیند ذوب به درستی کنترل نشود و به دقت ترکیب شیمیایی و دما تنظیم نشود ممکن است میلگردهای تولید شده ضعیف تر و مستعد ترک خوردن یا شکست در شرایط بارگذاری بالا شوند. به همین دلیل کورههای قوس الکتریکی و القائی که توانایی کنترل دقیق دما و ترکیب شیمیایی را دارند می توانند میلگردهایی با کیفیت بهتر تولید کنند.
به گفته آهن جم : قیمت روزانه میلگرد به روش تولید و کیفیت آن بستگی دارد . وقتی میلگرد با روش های استاندارد و با کیفیت بالا تولید شود قیمت بیشتری دارد که به علت کیفیت بیشتر میباشد. برای تولید میلگرد شمش های فولادی تحت فرآیند نورد گرم قرار میگیرند .
همچنین کیفیت میلگرد های تولید شده از ضایعات به میزان تصفیه و پالایش ضایعات قبل از ذوب بستگی دارد. در بسیاری از موارد ضایعات فولادی ممکن است حاوی ناخالصی هایی مانند گوگرد، فسفر یا دیگر عناصر مضر باشند که میتوانند به کیفیت نهایی محصول آسیب برسانند. اگر این ناخالصی ها به درستی از فولاد حذف نشوند میتوانند باعث کاهش استحکام، چقرمگی و انعطاف پذیری میلگردها شوند.
مواد اولیه تولید میلگرد
ضایعات فولادی
ضایعات فولادی یکی از اصلی ترین مواد اولیه برای تولید میلگرد هستند. این ضایعات میتوانند از صنایع مختلف مانند خودرو سازی، ساختمانی، ماشین آلات و حتی محصولات فولادی قدیمی بازیافت شوند. به دلیل این که فولاد مادهای قابل بازیافت است استفاده از ضایعات فولادی نه تنها به کاهش هزینههای تولید کمک میکند بلکه اثرات زیست محیطی را نیز کاهش میدهد. فرآیند ذوب ضایعات فولادی در کورههای قوس الکتریکی یا کورههای القائی فولاد مذاب با کیفیت بالا برای تولید میلگرد به دست میآورد. استفاده از ضایعات فولادی به عنوان ماده اولیه باعث صرفه جویی در مصرف سنگ آهن و منابع طبیعی میشود.
با این حال کیفیت میلگرد های تولید شده از ضایعات فولادی ممکن است به ترکیب شیمیایی و کیفیت ضایعات بستگی داشته باشد. ضایعات فولادی باید به دقت انتخاب و تصفیه شوند تا ناخالصی ها و مواد مضر مانند گوگرد، فسفر و مواد غیرفلزی از آنها جدا شوند. در صورتی که این ضایعات به درستی تصفیه نشوند میتوانند تأثیر منفی بر خواص مکانیکی و استحکام میلگردهای نهایی بگذارند. بنابراین استفاده از ضایعات فولادی نیازمند کنترل دقیق در هر مرحله از فرآیند تولید است.
شمش فولادی
شمش فولادی به عنوان یکی از مهم ترین مواد اولیه در تولید میلگرد به کار میرود. این شمشها معمولاً از فرآیند های تولید فولاد مانند کوره بلند یا کوره قوس الکتریکی به دست میآیند و به شکل قالبهای بزرگ و سنگین فولادی تولید میشوند. شمشهای فولادی پس از فرآیندهای مختلف مانند نورد گرم یا سرد به میلگردهایی با ابعاد مشخص تبدیل میشوند. استفاده از شمش فولادی در تولید میلگرد موجب میشود که محصولات نهایی از نظر ترکیب شیمیایی و خواص مکانیکی همگن تر و قابل پیش بینی باشند.
یک مزیت عمده استفاده از شمش فولادی این است که این ماده اولیه میتواند به راحتی به انواع محصولات فولادی دیگر مانند میلگرد، تیرآهن، پروفیل و دیگر مقاطع فولادی تبدیل شود. همچنین شمشهای فولادی به دلیل داشتن کیفیت بالاتر نسبت به برخی از ضایعات معمولاً میلگردهایی با استحکام و چقرمگی بالاتری تولید میکنند. از طرفی فرآیند تولید شمش فولادی نیازمند استفاده از منابع معدنی مانند سنگ آهن و کک است که این خود میتواند هزینههای تولید را افزایش دهد.
آهن اسفنجی
آهن اسفنجی یکی دیگر از مواد اولیه مهم برای تولید میلگرد است. این ماده از فرآیند احیای مستقیم سنگ آهن به دست میآید و نسبت به سایر منابع فولادی دارای میزان ناخالصی کمتری است. آهن اسفنجی به دلیل اینکه در دمای پایین تری نسبت به روشهای سنتی ذوب سنگ آهن تولید میشود فرآیند تولید آن انرژی کمتری مصرف میکند. این ماده به صورت قطعات اسفنجی یا تکههای کوچک تولید شده و میتواند به راحتی در کورههای قوس الکتریکی ذوب شود. آهن اسفنجی به دلیل کیفیت بالا و کم نقص بودن در تولید میلگردهایی با خواص مکانیکی مطلوب بسیار مؤثر است.
مزیت دیگر استفاده از آهن اسفنجی این است که این ماده میتواند جایگزین مناسبی برای استفاده از سنگ آهن در تولید فولاد باشد. به دلیل کیفیت بالاتر آهن اسفنجی میلگردهای تولید شده از آن معمولاً استحکام و خواص بهتری دارند. همچنین آهن اسفنجی به دلیل هزینه های تولید پایین تر نسبت به فولاد خام از نظر اقتصادی به صرفه تر است. این ویژگیها باعث میشود که آهن اسفنجی در صنایع فولاد سازی برای تولید میلگرد بسیار محبوب و پرکاربرد باشد.
قراضه فولادی
قراضه فولادی یکی از مواد اولیه بسیار مهم و اقتصادی برای تولید میلگرد به شمار میرود. قراضه فولادی شامل آهن قراضه از خودروها، ماشین آلات صنعتی، تجهیزات ساختمانی و دیگر محصولات فولادی قدیمی است که بهطور گسترده در کارخانههای بازیافت جمع آوری میشود. این ماده اولیه به دلیل این که فولاد 100 درصد قابل بازیافت است گزینه ای بسیار اقتصادی و دوست دار محیط زیست محسوب میشود. ضایعات فولادی پس از جمعآوری در کورههای قوس الکتریکی ذوب شده و به فولاد مذاب تبدیل میشوند که سپس برای تولید میلگرد مورد استفاده قرار میگیرد.
استفاده از قراضه فولادی به طور قابل توجهی هزینههای تولید را کاهش میدهد زیرا نسبت به استفاده از سنگ آهن، به منابع معدنی کمتری نیاز دارد. همچنین استفاده از قراضه فولادی در تولید میلگرد، علاوه بر کاهش هزینهها به حفاظت از محیط زیست نیز کمک میکند. به دلیل اینکه قراضه فولادی معمولاً حاوی ناخالصی هایی مانند فسفر یا گوگرد است لازم است که این ضایعات قبل از ذوب به دقت تصفیه شوند تا کیفیت محصول نهایی تحت تأثیر قرار نگیرد. در نتیجه استفاده از قراضه فولادی در صورتی که فرآیند بازیافت به درستی انجام شود میتواند منبعی بسیار مؤثر و اقتصادی برای تولید میلگرد باشد.
کدام مواد اولیه برای تولید میلگرد بهتر است ؟
اگر به دنبال تولید میلگردهایی با کیفیت بالا و استحکام بالا هستید شمش فولادی بهترین گزینه است. برای پروژههای با حساسیت کمتر یا زمانی که هزینه اهمیت بیشتری دارد ضایعات فولادی یا قراضه فولادی میتواند انتخاب مناسبی باشد بهویژه که فرآیند بازیافت آنها اثرات زیست محیطی کمتری دارد. آهن اسفنجی نیز انتخاب مناسبی برای تولید میلگرد با کیفیت متوسط و هزینه کمتر است.
برای تولید میلگرد، بهترین مواد اولیه به ترکیب شیمیایی و کیفیت فولاد نهایی بستگی دارد. به طور کلی هر ماده اولیه مزایا و معایب خاص خود را دارد، اما در نظر گرفتن شرایط خاص کارخانه و هدف تولید میتواند انتخاب بهتری را ایجاد کند. در اینجا بررسی اجمالی از مواد اولیه مختلف و بهترین گزینهها آورده شده است
شمش فولادی
این ماده اولیه معمولاً بهترین گزینه از نظر کیفیت است زیرا شمشها دارای ترکیب شیمیایی ثابت و به نسبت ناخالصی کمتری هستند. تولید میلگرد از شمش فولادی منجر به میلگردهایی با خواص مکانیکی بسیار پایدار و استحکام بالاتر میشود. به ویژه برای تولید میلگرد هایی که در پروژههای حساس و نیازمند استحکام بالا (مثل سازههای بلند یا پروژههای مقاوم در برابر زلزله) استفاده میشوند، شمش فولادی بهترین انتخاب است. با این حال هزینه تولید بالاتر و نیاز به منابع معدنی طبیعی از معایب این گزینه است.
آهن اسفنجی
اگر به دنبال یک گزینه با هزینه کمتر و تأثیرات زیست محیطی پایین تر هستید آهن اسفنجی میتواند انتخاب مناسبی باشد. این ماده معمولاً از احیای مستقیم سنگ آهن به دست میآید و نسبت به فولاد خام و شمش فولادی انرژی کمتری برای تولید نیاز دارد. میلگردهای تولید شده از آهن اسفنجی معمولاً کیفیت مناسبی دارند و برای پروژه هایی که نیاز به استحکام متوسط دارند بسیار مناسب هستند.
ضایعات فولادی
استفاده از ضایعات فولادی می تواند از نظر اقتصادی بسیار به صرفه باشد زیرا به طور کلی هزینه کمتری نسبت به استفاده از شمش فولادی دارد. علاوه بر این استفاده از ضایعات فولادی به حفاظت از محیط زیست کمک میکند و فرآیند بازیافت فولاد به طور قابل توجهی باعث کاهش مصرف منابع طبیعی میشود. با این حال کیفیت میلگرد های تولیدی از ضایعات به ترکیب ضایعات و فرآیند ذوب وابسته است و در صورت کنترل نکردن دقیق این عوامل ممکن است کیفیت نهایی کاهش یابد.
قراضه فولادی
مشابه ضایعات فولادی قراضه فولادی نیز به دلیل قابلیت بازیافت و هزینه کمتر بهعنوان ماده اولیه رایج در تولید میلگرد استفاده میشود. اما مانند ضایعات قراضه فولادی نیز باید به دقت تصفیه شود تا ناخالص یها از بین بروند. کیفیت میلگردهای تولیدی از قراضه معمولاً کمتر از شمش فولادی است اما به عنوان یک گزینه اقتصادی، در بسیاری از پروژهها به ویژه پروژه های کمهزینه و غیرحساس کاربرد دارد.
نتیجه گیری
تولید میلگرد از ضایعات فرآیندی پیچیده اما بسیار سودمند است که علاوه بر کاهش هزینههای تولید، تأثیر مثبتی بر محیط زیست دارد. این فرآیند شامل مراحل مختلفی از جمله جمعآوری، تفکیک، ذوب، پالایش، نورد و کنترل کیفیت است. استفاده از این روش علاوه بر بهینه سازی مصرف مواد اولیه به کاهش ضایعات فلزی و حفظ منابع طبیعی کمک شایانی میکند. از این رو سرمایهگذاری در فناوریهای بازیافت آهن و تولید میلگرد از ضایعات، گامی مهم در جهت توسعه پایدار صنعت فولاد محسوب میشود.
12158798